FILTRI IN LINEA AUTOPULENTI
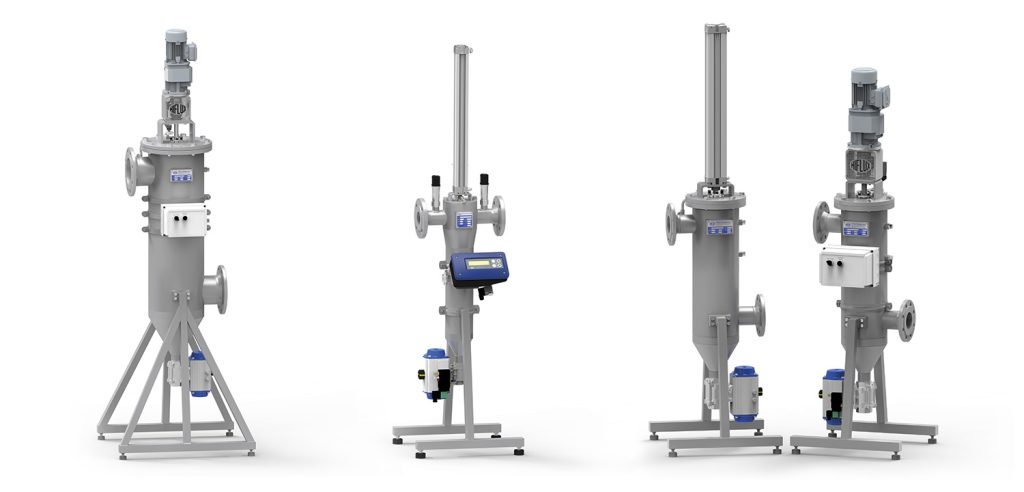
HIFLUX FILTRATION A/S
Vale a dire l’esperta in tutte le tipologie di filtri più note (filtri a sacco, filtri a cestello, filtri magnetici, filtri a cartuccia…etc.), ha ulteriormente introdotto sul mercato una novità assoluta nel campo della filtrazione:
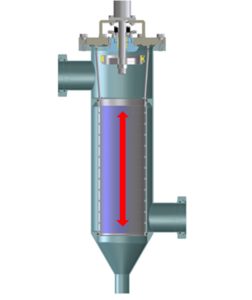
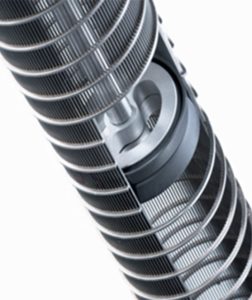
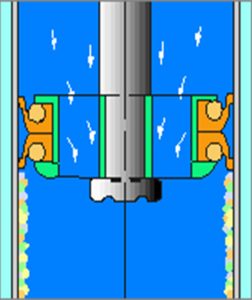
FILTRO AUTOPULENTE LINEARE
L’unità raschiante del filtro autopulente lineare (SCRAPER) a forma di disco è aperta nel centro in modo tale che il prodotto possa continuare a fluire senza ostacoli durante la fase di pulizia.
Pulisce la superficie interna del filtro circa 3/4 volte al minuto, spingendo il filtrato verso il cono di scarico.
Lo scraper è a ‘doppia azione’, quindi, pulisce in entrambe le fasi di discesa e salita.
Il materiale dello scraper del filtro può essere realizzato in diversi materiali, come ad esempio:
- PTFE rinforzato al carbonio
- PA (poliammide)
- PEEK (polietere etere chetone)
FILTRO AUTOPULENTE ROTATIVO
Le unità raschianti del filtro autopulente rotativo (SCRAPER) sono angolate e permettono il passaggio del prodotto durante la fase di pulizia.
L’intera superficie interna del filtro viene pulita circa 8 volte al minuto; il prodotto viene spinto verso il cono di scarico.
Materiali dello scraper del filtro:
- PEEK (polietere etere chetone)
- POM (poliossimetilene)
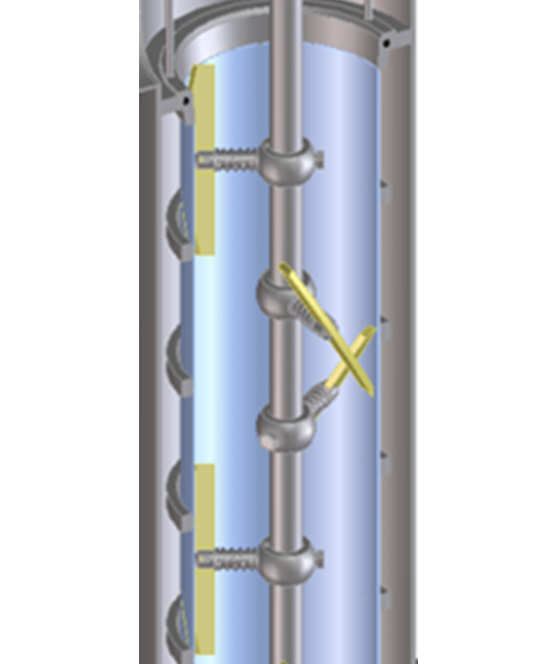
CARATTERISTICHE DEI FILTRI AUTOPULENTI
Filtrazione di particelle dure, soffici e fibrose.
Tre tipologie di elemento filtrante:
- wedge wire
- forato meccanicamente
- forato laser
Range di filtrazione: 30-2000 µm
La selezione del filtro autopulente viene fatta in base al tipo di prodotto, alla portata, alla viscosità, alla temperatura, al tasso di ’sporco’, se è un processo a batch o in continuo.
Nota: i filtri autopulenti non sono adatti alla filtrazione di particelle abrasive come sabbia e terra poiché gli scraper si consumerebbero troppo in fretta
ELEMENTI FILTRANTI DEI FILTRI AUTOPULENTI
Wedge wire
- Range: 30-2000 µm
- Filtrazione di particelle solide e dure
Forati Laser
- Range: 35-400 µm
- Adatto a tutte le particelle (anche fibrose e gel)
Forati meccanicamente
- Range: 500-3000 µm
- Adatto a particelle larghe
FORATURA LASER DELLE MAGLIE DEL FILTRO AUTOPULENTE
Vantaggi:
- fori conici: per prevenire il blocco di particelle
- filtrazione assoluta (+/- 10 µm)
- filtrazione di particelle dure, soffici/gel e fibre
OPTIONAL DEI FILTRI AUTOPULENTI
Camicia di riscaldo:
- per mantenere il fluido ad una T fissa in modo da garantire la stabilità/qualità del prodotto
- fino a 270°C
Sistema di sollevamento:
- sistema meccanico per accedere facilmente alla parte interna del filtro in modo da facilitarne le operazioni di manutenzione
- per mantenere il filtrato presente nel cono allo stato liquido e per evitare l’accumulo di particelle e il conseguente blocco
Filtro carrellato + pompa a membrana
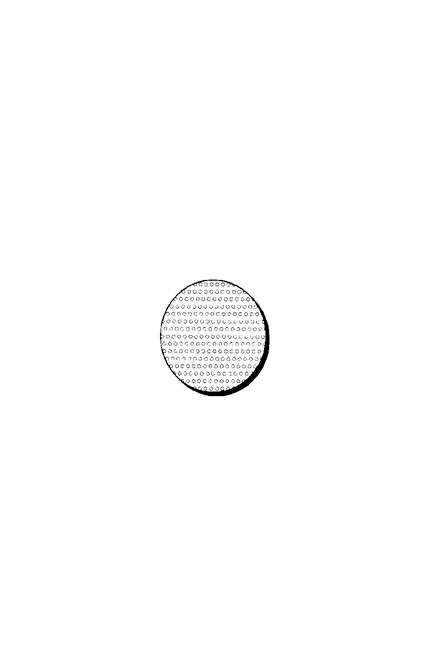
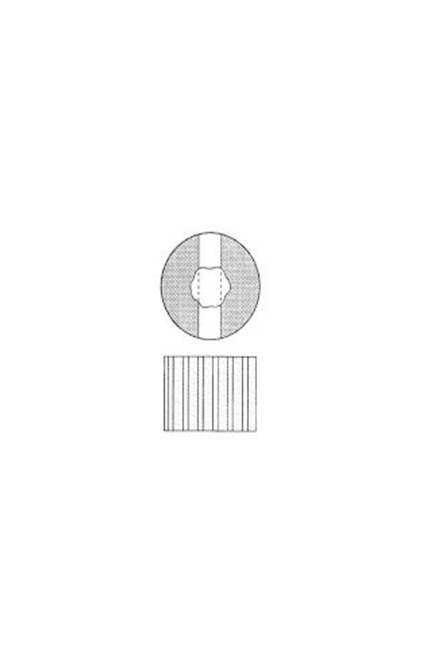
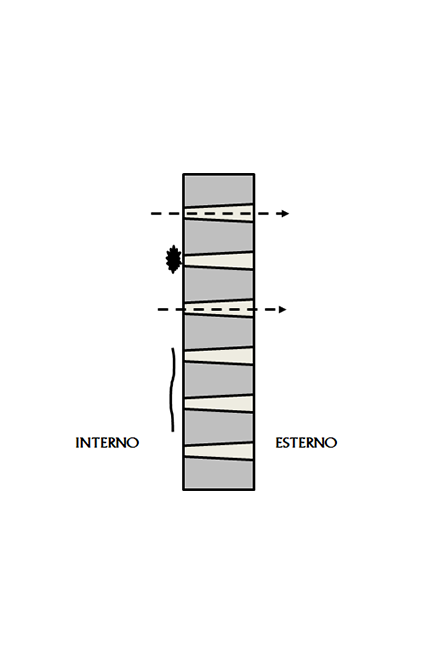
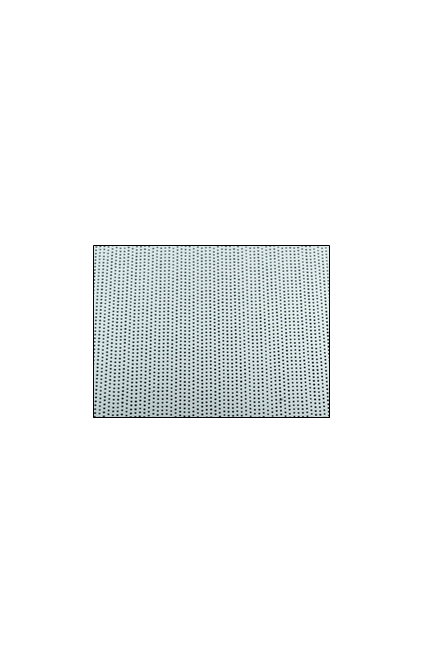
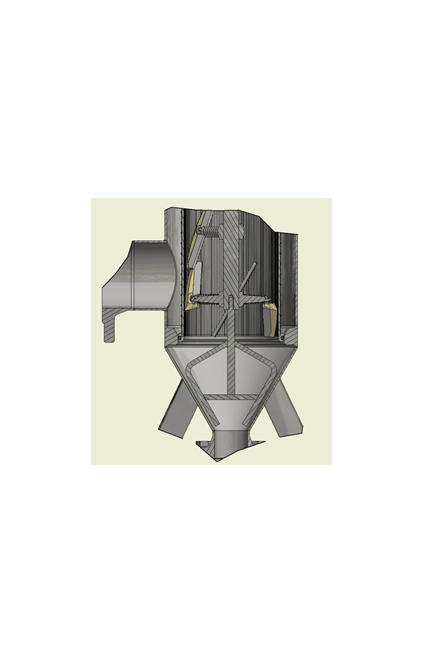

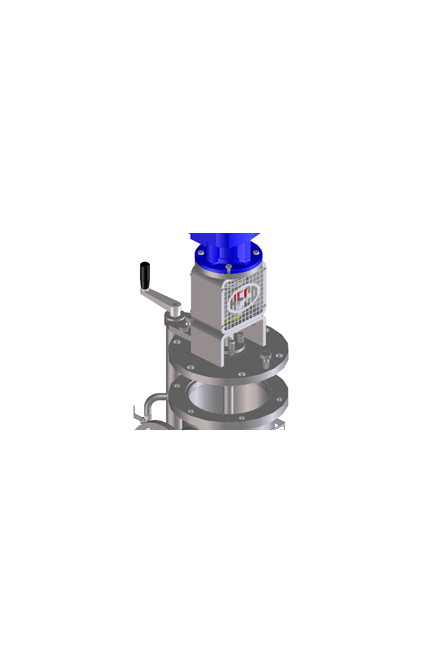
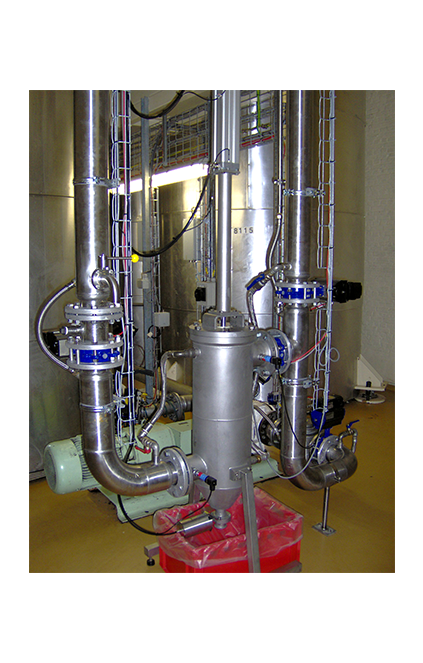
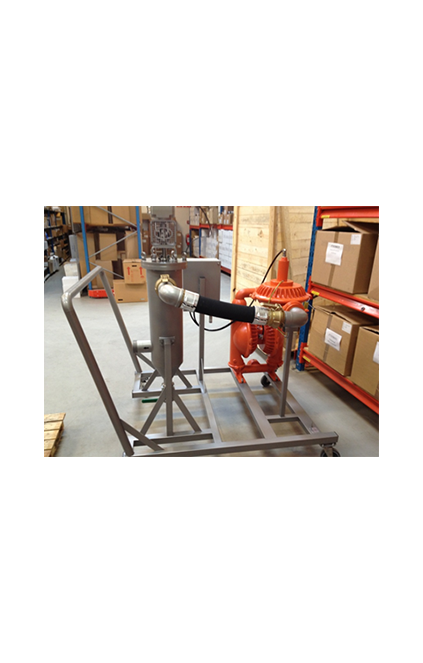
VANTAGGI DEI FILTI AUTOPULENTI
IL FILTRO AUTOPULENTE:
- In primo luogo, assicura un prodotto con sempre la medesima qualità
- Portata e taglia di filtrazione costante grazie alla continua azione raschiante
- Ritenzioni di particelle dure, soffici e fibrose
- Riduzione di perdita di prodotto
- Minori tempi di filtrazione, quindi, incremento della produttività
- Miglioramento dell’ambiente di lavoro
- Minor perdita di prodotto finito rispetto a filtri a sacco
- No fermo impianto dovuto dalla rottura/sostituzione del filtro a sacco o cartuccia
- Soprattutto, riduzione dei costi operativi rispetto a filtri manuali
- No ri-filtrazione dovuta dalla presenza di impurità nel prodotto finito
- Nessuno lotto rifiutato a causa della rottura del filtro a sacco
- Riduzione smaltimento rifiuti tossici/pericolosi, di conseguenza, minori costi di smaltimento
- Nessun contatto dell’operatore con prodotti ad alta temperatura o pericolosi
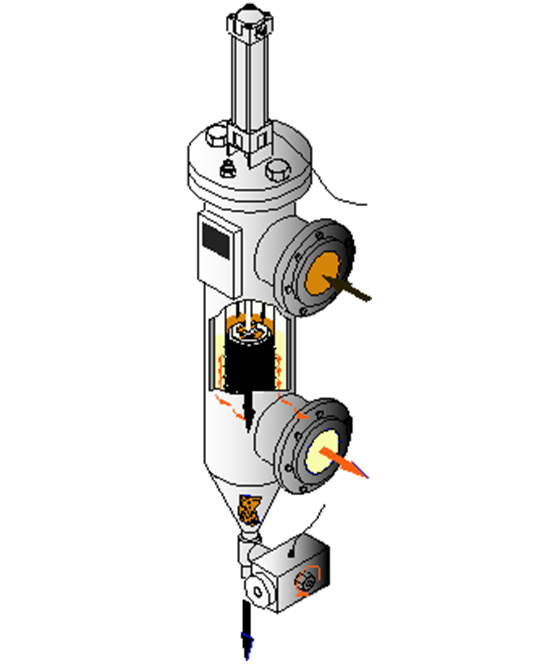
COME SCEGLIERE UN FILTRO AUTOPULENTE E PERCHÉ?
QUANDO E PERCHÉ UTILIZZARE IL FILTRO AUTOPULENTE CON SISTEMA A PISTONE
I filtri autopulenti con sistema a pistone hanno un miglior effetto filtrante nei seguenti casi:
- per produzioni in continuo
- quando la densità delle particelle da filtrare è simile a quella del liquido
- per basse percentuali di sporco, poiché la frequenza di pulizia è 3/4 volte al minuto
- per liquidi/particelle ‘shear sensitive’
QUANDO E PERCHÉ UTILIZZARE IL FILTRO AUTOPULENTE A SISTEMA ROTATIVO
I filtri autopulenti con sistema rotativo, invece:
- più indicato per produzioni a batch
- per alte percentuali di sporco (frequenza 8 volte/min)
- quando è richiesta una tenuta dell’albero migliore
- se ci sono problemi di ingombro
QUESTE SONO SOLO INDICAZIONI GENERALI…OGNI SPECIFICO PROGETTO VIENE VALUTATO AD HOC!
APPLICAZIONI DEI FILTRI AUTOPULENTI
I filtri autopulenti di Hiflux vengono utilizzati, per la filtrazione ottimale, principalmente per le seguenti applicazioni:
- Industria dei coloranti, vernici e coating
- Industria chimica (Inchiostri, resine, adesivi)
- Industria alimentare
- Industria dei polimeri
- Trattamento acqua
- Energia
- Industria farmaceutica
- Acque reflue
- Marino
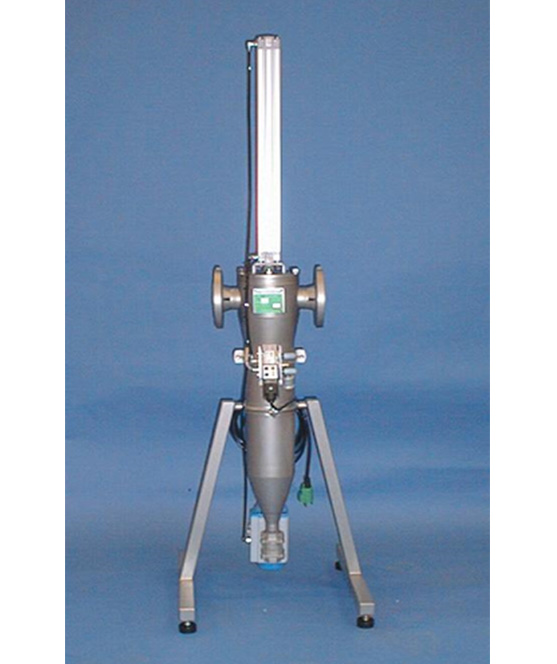
PROCESSI
PROTEZIONE
Componenti del processo contro danni derivanti dalle impurità:
- pompe
- scambiatori di calore
- valvole
- caldaie
- valvole di regolazione
- sfere di lavaggio
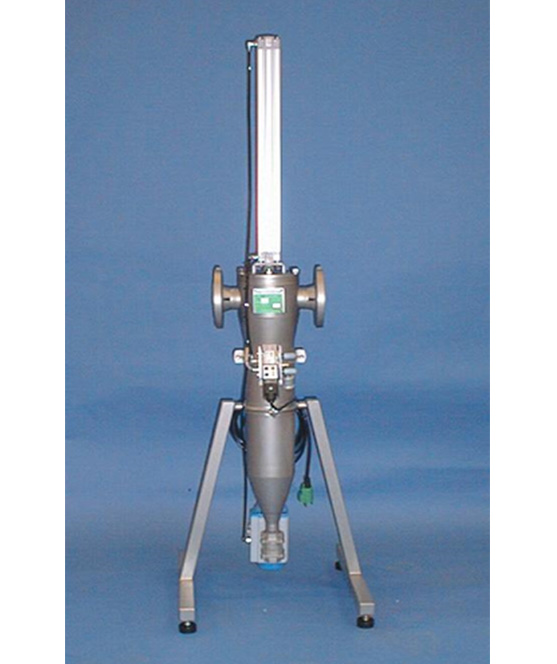
RAFFINAZIONE DEL PRODOTTO
- filtrazione del prodotto finale assicurando la qualità
- rimozione di particelle indesiderate e conglomerati
- ritenzione di particelle desiderate nel fluido
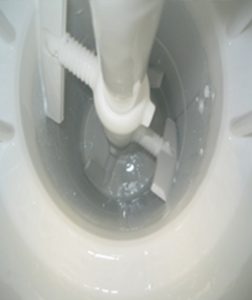
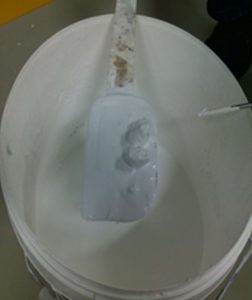
CASE HISTORY
Application:
Filtration of:
- Egg-white (was 800 µm, requires100 µm)
- Egg yolk (was 1000 µm, requires 500 µm)
- Complete egg (was 1000 µm, requires 500 µm)
Case:
Problems with linear self-cleaning filters:
- Production downtime due to filter cleaning
- Too much dirt through the filter (costs for centrifuges)
Goal
- 16 hours non-stop production, then CIP cleaning
- Less dirt to centrifuges (saving on maintenance costs, or remove centrifuges)
Solution:
- Auto-line XLR-E in hygienic design
- 100 µm laser bore element
- 500 µm perforated elements
- PEEK cutting edge vertical scraper knives
Application:
Pre-filtration of condensate water before UF and RO-installation.
Case:
The client wants to replace manual bag filters with an automatic filtration solution. Peaks and drops in process pressure during draining of filter are not acceptable.
- Flow requirement: 160 m³/h continuous
- Design pressure: 16 bars
- Filtration: 35 microns
- Particles: organic/soft components & burnt sugar
Solution:
The system consists of a HiFlux Auto-line XXLE self-cleaning filter in hygienic design. The filter is equipped with extended cylinder, 35-micron laser bore screen and DN25 butterfly drain valve with slow open/close feature. Installation was made in 2015.
Application:
Filtration of recirculated water on production line for home-cheese.
Case:
The client is filtering the water through a filter cloth (8 x 2 m), which is fixed to a tub on the production line. The cloth can’t be removed from the tub, and the client is cleaning the cloth manually. Client wants to limit this difficult and labour-intensive cleaning process.
- Flow: 18 m³/h
Solution:
A HiFlux self-cleaning filter type Auto-Line M with ∆P controller type ECII was installed as a prefilter to the cloth. This reduced the dirt load on the filter cloth and limited the time needed for cleaning considerably.
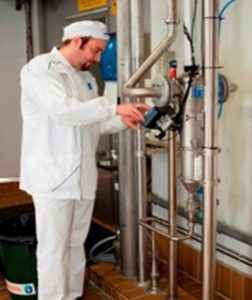
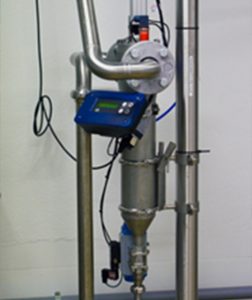
Application:
Filtration of whey
Case:
The client requires automatic filtration of whey concentrate in order to remove burned particles from the pipe work.
- Viscosity: 500 cP
- Flow requirement: 63 m³/h
- Filtration: 50 microns
Solution:
The system consists of a HiFlux Auto-line LE self-cleaning filters with extended cylinder, 50-micron wedge wire screen and drain with sluice system for reduced product loss. Installation was made in 2013.
Application:
Filtration of whey in a cheese factory.
Case:
- Flow: 12 m3/h
- Filtration: 100 microns
Solution:
The system consists of 1 pc. Auto-line XLE with a ∆P controller, 100 µm wedge wire strainer and a sluice system. The product has a lot of small cheese parts in it, which is filtered out as it may be used as food.
The media is the whey with curd particles which are the residual from pressing the cheese into moulds. The cheese parts, which are carried over with the whey, are retained in the filter and through the sluice system, the cheese parts are concentrated with a high degree of dry matter.
The filtered whey is forwarded to the membrane filtration system for further processing.
Quantity filtered out is 1000 kg/week.
The filter is set to scrape at a low differential pressure in order not to break up the brittle cheese parts in to smaller parts. Drain is set to a relatively high setting to avoid losing too much whey.
Application:
Filtration of brine from brine cages to remove cheese particles from the brine before recycling.
Case:
- Flow: 60 m3/h
- Filtration: 100 microns
Solution:
Auto-line XLE with 100-micron filter element in sanitary design.
Application:
Filtration of un-dissolved milk powder particles from batch mixing of water and powder at 75°C
Case:
Client want to replace existing centrifuge and 40-micron cartridge filtration, due to high maintenance cost and cartridge disposal.
- Capacity requirement 20 m³/h.
Solution:
After successful testing with an Auto-line M, the final order was specified for an Auto-line LE with sanitary design and 50-micron laser element. The Auto-line filter replaced the centrifuge and cartridge filters, resulting in fully automatic ∆P operation and reduced maintenance and spare parts costs.
Application:
Filtration of salt brine in a cheese dairy
Case:
- Flow: 70 m3/h
- Viscosity is slightly higher than water at around 13½oC and a salt concentration of 18%
Solution:
The system consists of 1 pcs. Auto-line XL with a ∆P controller and a 100 µm wedge wire strainer. The product has a lot of small cheese parts in it which is filtered out. The filter is set to clean at a low differential pressure in order not to break up the brittle cheese parts in to smaller parts. Drain is set to a relatively high setting to avoid losing too much brine. Quantity filtered out is 2-5 kg/day.
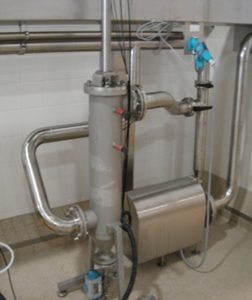
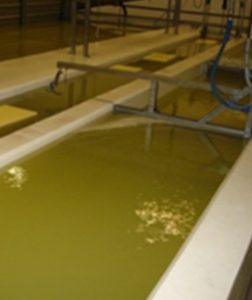
Application:
Filtration of viscous rework cheese before moulding and cutting to sliced cheese.
Case:
- Flow: 1000-2500 kg/h
- Process temperature: 60-80°C
- Filter positioned just after mixing/cooking tank, therefore no heating jacket needed.
Solution:
The system consists of 1 pcs. Auto-line MLR-E Melt Cheese Filter in hygienic design, equipped with 4-channel scraper system and 300 µm laser bore filter element.
Application:
Filtration of condensate from creamery prior to reverse osmosis plant.
Case:
The purpose is to remove casein carried over in the evaporation stage.
The filters have replaced the bag filters thus decreasing the need for manual work during 20 hours shifts.
Solution:
The system consists of 2 pcs. HiFlux Auto-line XLE self-cleaning filters with extended cylinders, electronic ∆P controller and 30 µm wedge wire strainer. Installation was made in 2005.
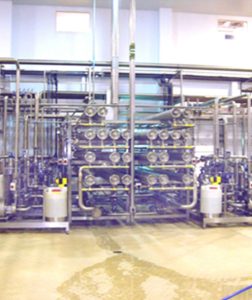
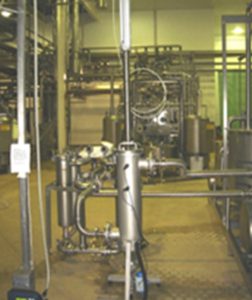
Application:
Filtration of different types of potato starch for use in the paper industry.
Case:
The processing system comprises many kilometres of piping and many components which are flushed with CIP liquids frequently.
The client requires automatic filtration of the CIP liquids before reuse.
Filtration requirement:
- 150 microns
- Flow: 55 m³/h
Solution:
HiFlux self-cleaning filter type Auto-line XL.
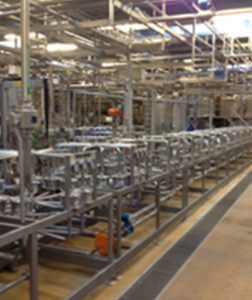
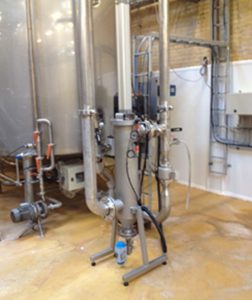
Application:
Filtration of chocolate rework from biscuit production.
Case:
Client was using a vibrating screen with 1 mm filtration to filter the chocolate, and would like to automate due to:
- Manual cleaning of the screen
- Clogging of the nozzles
- Filter positioned just after mixing/cooking tank, therefore no heating jacket needed
Dirt: biscuit dust app. 20 l / day
Flow: 3 – 6 m³/h
Temperature: 45 – 60°C
Solution:
Auto-Line LE self-cleaning filter with:
- Heating jacket
- Extended cylinder
- Automatic ∆P filter operation
- Water heated sluice chamber for minimized product loss
- Filtration degree 300μm wedge wire
Application:
Filtration of white and dark chocolate in a plant in operation since 2008.
Case:
Filtration of white and dark chocolate before loading on tanker trucks.
Solution:
The system consists of 2 pcs. Auto-line XLE self-cleaning filters in sanitary design, equipped with extended cylinder and heating jacket (hot water).
The filters are equipped with 500 µm wedge wire inserts designed for up to 8 bar delta P and 2” butterfly drain valves.
Application:
Filtration of white chocolate in a plant in operation since spring 2006.
Case:
Filtration of white chocolate with a viscosity of 5000 cP in order to retain solids thus securing the quality.
After filtration the product is loaded in to heated tanks for further transportation.
Solution:
The system consists of 1 pcs. Auto-line LE in sanitary design, equipped with extended cylinder, heating jacket (hot water) and electronic ∆P controller type ECII.
The filter is equipped with 500 µm perforated strainer in sanitary design and 2” butterfly drain valve.
Flow rate is 10-12 m3/h at a differential pressure of 0,5 bar at 5000 cp. Cleaning is set at 0,7 bar differential pressure.
Application:
Filtration of beer wort.
Case:
The brewery wants to remove insoluble hops particles from the beer wort. It is a batch production setup and product loss is a concern.
- Filtration required: 0,5 mm.
- Flow: up to 35 m3/h.
Solution:
The system consists of 1 pc. Auto-line XLE in hygienic design, equipped with extended cylinder and electronic ∆P controller.
The filter features ø 0,5 mm perforated strainer and a 15 litres sluice vessel with 2 pcs. drain valves. The sluice drain system reduces product loss and prevents pressure drops in the system. In operation since spring 2012.
Application:
Filtration of beer after dry hopping process.
Case:
The dry hopping of the beer is performed in a recirculating process, and the brewery wants to remove oversize hops particles from the beer before filling. It is a batch production setup and product loss is a concern.
- Filtration required: 150 micron.
Solution:
The system consists of 1 pc. Auto-line MLE self-cleaning filter in sanitary design, equipped with an extended cylinder. The filter features 150-micron wedge wire element and a sluice vessel with 2 pcs. drain valves.
Application:
Hot syrup of sugar beets builds burned scaling (sugar coal) on the pipe wall. The sugar coal particles, up to 10 mm size, must be removed.
Case:
Client was using bag filters and operators had to replace bags 24/7, especially at beginning of the season. Pipes etc. are very hot for operators to touch.
- Viscosity: 30-40 Brix
- Flow: 100 m3/h (reserve to 300 m3/h)
- Temperature: 110-135°C
Solution:
The system consists of 2 pcs. Auto-line XXLR-E with DN200 manifold for even distribution of the flow.
The filters are equipped with 1,5 mm perforated strainers, and 4 pcs. pneumatic butterfly valves for possibility to shut off a single filter for maintenance.
Each filter is equipped with sluice system with double automatic valves and sight glass.
Application:
Filtration of 98°C water with small seeds.
Case:
Client want to replace existing manual filter with 100-micron strainer because the employees wouldn’t/couldn’t empty the strainer due to high temperature and smell.
Operating pressure: 3-4 bar.
Solution:
HiFlux Auto-line LR-P rotating self-cleaning filter with:
- Pneumatic operation
- Oscillating controller
- Sluice system with separate timer for drain control
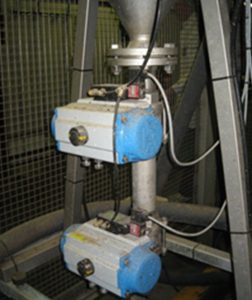
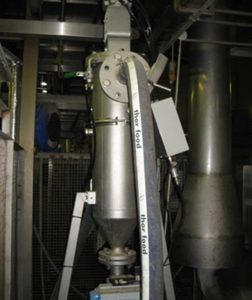
Application:
Filtration of sea water in a fish factory.
Case:
Sea water with fish is pumped into the fish factory, and the return flow must be filtered before pumping it back into the sea. The purpose is to filter out salmon louse, proteins and fish scales.
- Flow: 150 m³/hour
- Operating pressure: 2,0-2,5 bar
- Filtration requirement: 200 µm
Solution:
The system consists of 1 pcs. Auto-line XXL with and electronic ∆P controller. Filtration with a 200 µm laser drilled filter element.
Application:
Filtration of animal fats:
- before centrifuge
- before end filtration
Case:
- Eaton filter bags are installed. Too many times filter bags exchanging during process. High maintenance costs on centrifuges
- End filtration (police filter)
Solution:
- HiFlux Auto-line XLR-E, sanitary design, with vertical PEEK scraper knifes (to cut the plastic parts), 2000-micron perforated element sanitary design.
- HiFlux Auto-line XLR-E, sanitary design, Linear design, 50-micron laser-bore element, sanitary design.
Application:
Filtration of lecithin at truck offloading
Case:
Client wants to filter the lecithin (a food additive) during offloading of 30 tons trucks.
- Particles size: > 1mm micron.
- Dirt load: 4 kg dirt per truck.
Solution:
HiFlux Auto-line XLR-E self-cleaning filter, with 1000-micron perforated filter element and 2” ball valve (hand operated).
Application:
Filtration of fat and gelatin suspension in 2 different position in the manufacturing process.
Case:
First application is filtration of fat which is separated as a fraction of the initial boiling process of the pig skin. The filter retains all rest of pig skin which is returned to the reactor.
- Flow: 15 m3/h.
In the second application, the filters secure that the part of the pig skin in the waste is retained and subsequently returned to the reactor.
- Flow: 35 m3/h.
Solution:
The system consists of 2 pcs. Auto-line L self-cleaning filter with controller integrated in the factory SRO system.
Application:
Filtration of fat fraction from a process plant for animal by-products
Case:
The client wants to secure the quality of the product by removing plastic tags and bone fractions from the fat.
The product is hot and viscous and with a moderate content of solid material.
Solution:
A self-cleaning Auto-line XL filter with Ø 500 µm perforated strainer was installed. A sluice system is mounted in the drain to concentrate dry matter in the sludge as much as possible. Installation was made in 2003.
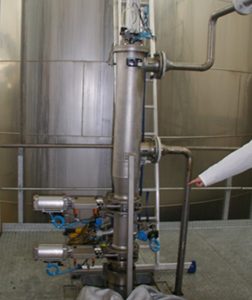
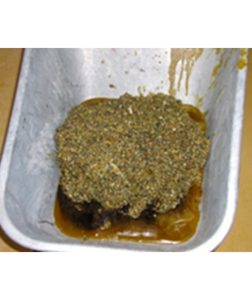
Application:
Filtration of raw imported honey as first treatment in order to remove larger impurities from the product.
Case:
The honey is supplied from overseas in tanks and is heavily loaded with unwanted particles.
- Flow: 3000 kg/h
- Operating temperature: 50°C
- Viscosity: 8000 mPas
Solution:
2 pcs. Auto-line XLE self-cleaning filters equipped with 200 µm perforated laser elements. Each filter has a capacity of 1500 kg/h. By using the Auto-line a homogeneous product is obtained which can be used without interruption in the following process.
Application:
Filtration of washing water on a food factory, where they produce canned foods.
Case:
Filtration of the washing water they use for washing of the cans, before they go into the Autoclave, so they can reuse the washing water.
Solution:
Auto-line ML self-cleaning filter with 200-micron laser bore filter element. The company saves about 8.500 euro per year on each washing line.
Application:
Filtration of blood in a slaughter house
Case:
Flowrate 30 tons per day.
Client wants to take animal ear marks, projectiles, hair from the pigs and some small pieces of rope out of the blood, before the blood is heat treated for selling to animal food production.
Solution:
HiFlux Auto-line LR-E self-cleaning filter with Ø 5 mm perforated filter element.
Application:
Continuous filtration of frying oil in a food industry company.
Case:
The oil is used for pre-frying batter coated chicken nuggets for a large fast food company. Some of the batter pollutes the frying oil and needs to be removed.
- Flow: 50 m3/h
- Temperature: 200°C
Solution:
HiFlux AKS 137 DN80 self-cleaning scraping filter with heating jacket and 100 µm wedge wire strainer.
Application:
Filtration of protein suspension in white spirit
Case:
Client wanted to remove rest protein before evaporation and re-condensation of the alcohol.
- Flow rate 3 m3/h
Solution:
Auto-Line M self-cleaning filter with 50-micron wedge wire filter element.
CERTIFICAZIONI DEI FILTRI AUTOPULENTI
I filtri autopulenti di Hiflux dispongono di diverse certificazioni.
Questo permette ai nostri filtri di rispettare le sempre più stringenti norme del settore sanitario.
- I filtri autopulenti sono realizzati in accordo alle direttive EC per sistemi sotto pressione PED 2014/68/EC e può essere fornito in accordo alle categorie I, II, III o IV
- Disponibile la versione ATEX, zone 1/21 e 2/22, in accordo alla direttiva 94/9/EC
- In accordo alla direttiva EC1935/2004 e FDA standard per polimeri ed elastomeri. Tracciabilità totale dal produttore fino al cliente finale, certificato dalla Danish Food Authorities
- I filtri autopulenti sono progettati secondo le linee guida dell’EHEDG